TM 43-0139
2-5. Sealing Compound, Curing (MIL-S-11031)
a.
Characteristics. This sealing compound is a two-part material consisting of a black polysulfide base compound
and a catalyst to be mixed according to instructions. This compound and the catalyst are contained in a two-compartment
container. After curing, the compound forms a rubber-like material and provides satisfactory adhesion.
b.
Use. This compound is used for sealing and plugging exposed holes in fire control instruments, such as holes for
setscrews, adjusting screws, and slugs that are accessible from the outside of the instrument.
c.
Curing.
WARNING
The catalyst used in this sealer contains a lead compound. Avoid contact with skin.
Wash hands after use.
The compound cures in 72 to 96 hours at approximately 80°F (27°C).
2-6. Sealing Compound, Noncuring (MIL-S-11030, Type I, Class I)
a.
Characteristics. This is a homogenous, stable, noncorrosive, and nontoxic compound. It is thermoplastic and
noncuring, and is not affected by oil or temperatures between -65°F to 180°F (-53.89°C to 82.22°C).
b.
Use. It is used for the static sealing of glass to metal instruments and to cover visible headless screws (except
adjusting screws). The compound is to be applied prior to painting.
2-7. Filler, Graduation or Engraving (TT-F-325)
a.
Characteristics. This is a paste-paint type filler that adheres firmly to the surface to which it is applied. It is issued
in black, deep red, white, and translucent white colors. It provides maximum legibility on graduated scales.
b.
Use.
(1)
For filling in the engraved graduation scales of instruments.
(2)
For small-arms sight graduations.
(3)
To replace similar material to equipment that has been removed by cleaning operations.
c.
Application. Fill the indentations with the paste by brushing, then wipe across the indentations with a cloth or
small knife blade. This action will press the paste into the indentations and remove most of the excess paste. Wash the
remainder from the surface before it sets with soap and water; rinse with clear water and allow to dry.
d.
Drying Time. Air-dry for 12 hours before handling. For the filler to dry hard, air-dry for 24 hours. A finish coat may
be applied over the graduated element after the filler has air-dried for 2 hours.
2-2
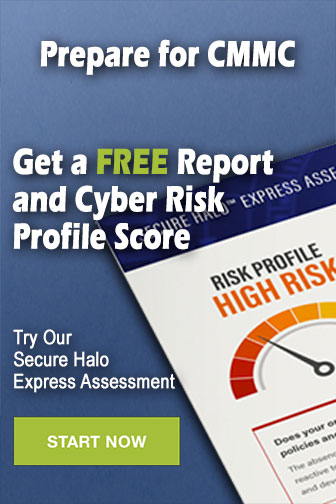