TM 43-0139
overload protection should be furnished for the electrical circuit; compressors should be located in an adjacent room and
not in the paint shop, as this reduces the fire hazard considerably, improves the performance of the compressor, and
reduces operator fatigue caused by the compressor noise; permanent installations should be at least one foot from
adjacent walls to allow free air circulation over the cooling fins; air intakes should be piped to the outside of the building,
where they can pick up clean, cool air; air pipe lines should be of sufficient size; an air compressor should be mounted on
a solid foundation, because unless the weight is equally distributed, excessive vibrations will result in noisy operation and
may cause a break in the tank supports or the compressing equipment; and the compressor should be installed so that it
is level, with regard to a horizontal tank, and plumb, in the case of a vertically mounted tank, as this will assure the proper
function of the compressor oiling system.
(b)
Replacement. Like all mechanical devices, air compressors eventually wear out and should be
replaced or rebuilt when: operational efficiency has decreased through wear and mechanical adjustments fail to restore it;
or there is an insufficient air output which cannot be corrected by normal equipment adjusting; or the time interval from
cut-in to cut-out is prolonged to the point of wasting power (a 50 percent deviation from the expected time interval is
sufficient reason for replacing or rebuilding the system).
(c)
Draining. The operation of compressing air, which always contains some moisture, induces
condensation. Water condensed in this manner collects in the air receiver of the compressing outfit and must be removed
each day by draining through the air receiver petcock. Proper location of the air intake will cut down the amount of water
condensed in this manner.
(d)
Servicing. Servicing of air compressors by personnel should be confined to the instructions given in
this paragraph. Any further servicing by maintenance personnel should be performed in accordance with Technical
Manuals on the specific compressors.
b.
Tanks (Paint Containers).
(1)
General. Material containers for spray painting systems are metal or glass vessels which are connected to
the spray gun. These containers serve as supply reservoirs for the material to be sprayed, and are of a cup or tank type.
CAUTION
Painters planning to use coatings formulated with chlorinated solvents (such as MIL-C-46168,
Type III) must remove all aluminum components from their painting system and replace with
aluminum-free or stainless steel parts.
(2)
Cup containers. Containers of this type are generally used where a variety of colors in rather small
quantities are to be sprayed. There are two types: suction and pressure feed. Pressure-feed cups are recommended for
small quantities of enamels, plastics, and other materials too heavy for suction feed, and where fine adjustment and
speed of application are desired. The commercial preloaded and precharged pressure spray cans are unrechargeable.
(3)
Tanks. Spray gun tanks are material containers for pressure-feed systems and provide a constant flow of
paint at a uniform pressure. Their capacities range from two to 55 gallons. They consist of a container with a clamp-on
lid, a fluid tube, outlet valves, a pressure gage, an agitator, and a safety valve. They also have an insertable paint
container. They are furnished with either a top or bottom outlet and various accessories. There are two distinct types:
Regulator type tanks offer the advantage of supplying large quantities of material to the gun under accurately controlled
fluid pressure. Regulator-type tanks are frequently further subdivided into single and double regulator types, depending
on whether the control is applied to the material pressure alone or to both the material and gun pressures. Regulator-type
tanks are equipped with a pressure regulator, safety valve, release valve, etc., and are operated with different pressures
on the air line and material. Equalized pressure tanks are equipped with only a safety and release valve, and operate with
the same pressure on the air line and on the material.
5-18
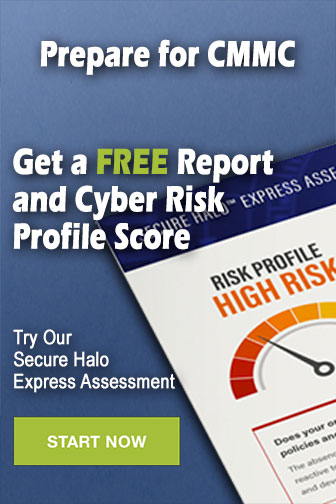